Wartung gemischter Flotten: Auf Nummer sicher zu gehen, kann teuer werden
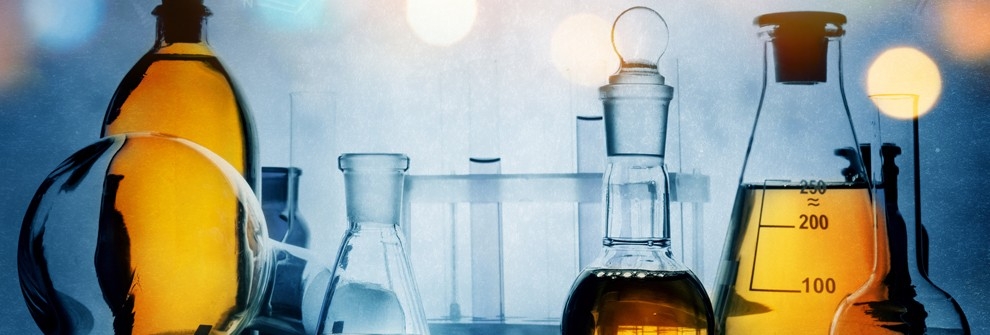
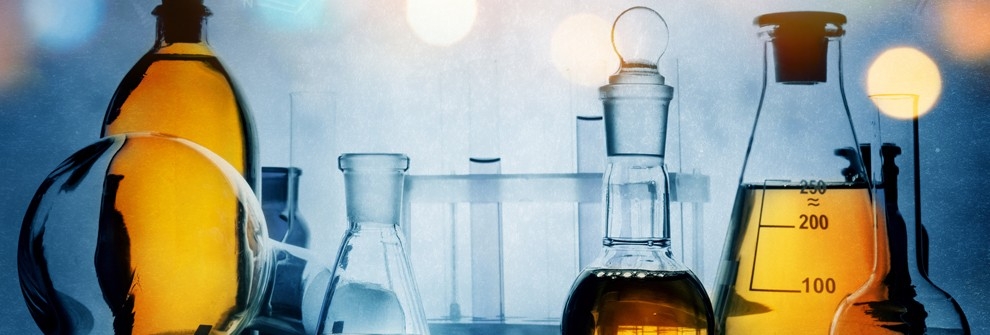
In Gesprächen mit Wartungsmanagern für Baugeräte ist klar geworden, dass gemischte Flotten mittlerweile die Norm sind. Die meisten geben an, dass der interne Kostendruck und Schwankungen in der Ausrüstungsqualität zwischen Herstellern die Hauptgründe sind, warum man nicht mehr einem einzigen Hersteller die Stange hält.
Obwohl gemischte Flotten Kosten senken und zuweilen die Leistungsfähigkeit verbessern können, gibt es doch Abstriche – am gravierendsten ist eine dramatisch verkomplizierte Wartungsplanung. Verschiedene OEMS haben unterschiedliche Spezifikationen für Service- und Wartungsintervalle, unterschiedliche Anforderungen und andere Schmierstoffvorgaben, wodurch Wartung zu einem schwierigen Balanceakt wird.
Wie kann man sich da durchschlagen? Viele Manager verfolgen bei Wartungsplänen und Ölwechselintervallen einen konservativen Ansatz und versuchen, ein gemeinsames Intervall zu finden, dass in der ganzen Flotte funktioniert. Doch nur all zu oft führt das dazu, dass Services und Ölwechsel häufiger als nötig – und unter den OEM-Empfehlungen durchgeführt werden. Diese konservative Planung, so die Begründung, ist eine billige „Versicherungspolice“, die ihrer Meinung nach die Notwendigkeit regelmäßiger Ölanalysen hinfällig macht.
Was diese Manager nicht verstehen, ist, dass bei der Ölanalyse nicht nur um das Öl geht. Durch eine Ölanalyse können Sie viele Arten von Problemen bei Ihrer Ausrüstung identifizieren – liegt eine Kraftstoffverdünnung vor, Verunreinigung durch Schmutz, tritt Kühlmittel aus oder besteht eine sonstige Problematik, die sich leistungsmindernd auswirkt. Ölanalysen helfen Ihnen, unerwartete Ausfälle von Ausrüstung vorherzusagen und möglicherweise zu vermeiden.
Durch die Einrichtung eines gemeinsamen Wartungsplans für die gesamte Flotte, und durch den Wegfall von Ölanalysen können Sie Material- und Arbeitskosten, gleichzeitig aber auch das Risiko katastrophaler Ausfälle an einzelnen Maschinen um gut 11 % erhöhen.
Nehmen wir einmal eine gebräuchliche Maschine wie einen Schürfzug. Ölwechsel, einschließlich der Kosten für das Öl, Filter, Altöl und Laborarbeiten kosten jährlich ca. € 1.400. Sind beispielsweise 100 ähnliche Maschinen in der Flotte, die vier Mal jährlich einen Ölwechsel erhalten, schlagen die Schmierstoffwechsel jedes Jahr mit € 141.000 zu Buche. Durch regelmäßige Ölanalysen könnte man sich im Mittel mindestens einen Ölwechsel pro Maschine pro Jahr sparen. Mit anderen Worten: ohne regelmäßige Ölanalyse werden jedes Jahr € 35.000 zu viel ausgegeben. Ganz zu schweigen von den Ausfallzeiten, die teurer sein können als die Einsparungen bei Materialkosten.
Ohne regelmäßige Ölanalysen nimmt man sich außerdem die Möglichkeit, üblicherweise auftretende Störungen an Maschinen vorhersagen zu können. Beispielsweise haben 40 % aller Motorausfälle mit einer Verunreinigung des Kühlsystems zu tun, was mit einer Ölanalyse festgestellt werden könnte. Wie hoch sind typischerweise die Kosten für den Austausch oder die Reparatur eines durch Kühlmittel beschädigten Motors? Im Schnitt sind das, sagen wir einmal, € 82.000. Gehen wir dann noch von einer unerwarteten Reparatur pro Jahr zu € 82.000 aus. Zuzüglich zu den bereits angefallenen € 35.000 kostet einen diese „billige Versicherungspolice“ dann gut und gerne € 120.000 pro Jahr.
Ein umfassendes Präventivwartungsprogramm, das es ermöglicht, alle vom OEM verlangten Intervalle zu verfolgen, Wartung entsprechend zu planen, und das regelmäßige Ölanalysen beinhaltet, kann den Schmierstoffverbrauch im Durchschnitt um 25 % senken und zudem zu einer größeren Verfügbarkeit und Nutzung der Maschinen führen. Die richtige Maschine kann zur richtigen Zeit gewartet werden, und man wird vor potenziellen Ausfällen gewarnt, bevor diese auftreten. Dadurch sinken nicht nur die Materialkosten, sondern werden auch die Produktivität optimiert und die Rentabilität jedes Fahrzeugs maximiert.
Wie sieht nun ein heute etablierte Programm im Vergleich zu einem Programm aus, wie es wünschenswert wäre?