Optimieren Sie Ihren Fuhrpark? Oder setzen Sie ihn Gefahren aus?
Viele Flotten kaufen bekannte Markenschmierstoffe, die nicht notwendigerweise auf ihre spezifischen Anwendungen zugeschnitten sind.
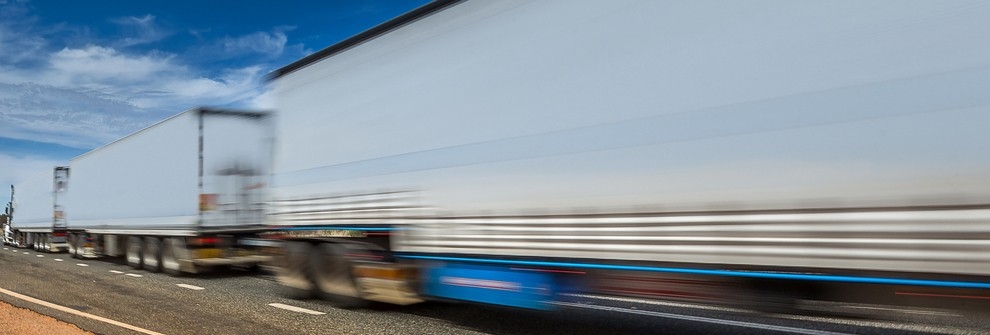
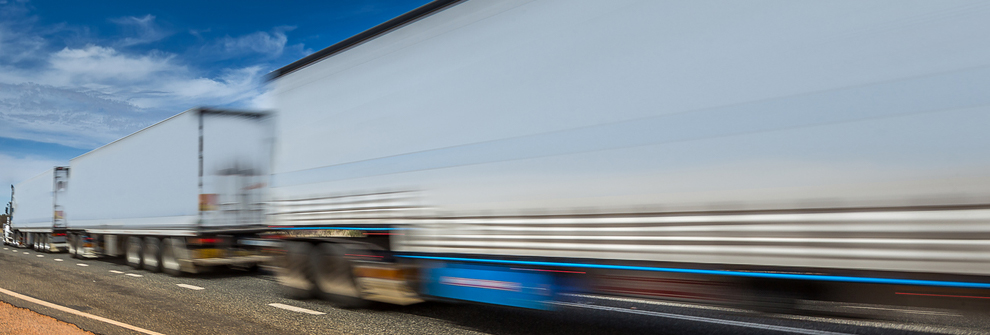
Einer unserer ehemaligen Kunden in Kanada hat vor kurzem seine Unabhängigkeit an einen Wettbewerber verloren. Angesicht knapperer Budgets begann man, Entscheidungen nur nach dem Preis zu treffen, auch billigere Öle zu verwenden und in der gesamten Flotte sich an typische Wartungsprotokolle zu halten. Mit diesem Ansatz sparten sie jedoch kein Geld, ganz im Gegenteil – es kam zu unplanmäßigen Ausfallzeiten von Anlagen und erhöhten Wartungskosten. Schließlich mündete der Schneeballeffekt in unzuverlässige Abläufe und in Kundenrückgang. Letztendlich wurde es ein nicht mehr profitables Unterfangen und es blieb keine Wahl als das Unternehmen aufzugeben. Die neuen Eigentümer pickten sich die Rosinen aus der Flotte und dem Personal und liquidierten die restlichen Ressourcen.
Ihre Geschichte ist ein Musterbeispiel für Flottenbetreiber auf beiden Seiten der Grenze. Wir sehen viele Flottenmanager, die bekannte Markenschmierstoffe kaufen, die nicht notwendigerweise auf ihre spezifischen Anwendungen, Betriebsbedingungen oder Wartungsziele zugeschnitten sind, die von Flotte zu Flotte variieren können. Dieser Ansatz hat zur Folge, dass Flottenmanager weder die Ölwechselintervalle, noch die Kraftstoffeffizienz oder Ausfallzeiten optimieren. Und in der Folge schlichtweg Geld verlieren.
Schauen wir uns einmal ein anderes Unternehmen an, das eine Bewertung seiner Schmierungspraxis durchführen ließ. Die Flotte des Unternehmens bestand aus 1.000 Lkw der Klasse 8, deren Ölwechselintervalle bei 56.000 km lagen. Durchschnittlich gab es bei ihnen zwei bis drei Ölwechsel und neue Filtersätze pro Fahrzeug pro Jahr, wobei jeder Lkw im Mittel 41 Liter Motoröl für etwa € 1,81 pro Liter benötigte. Ein für Wartungszwecke verlorener Tag kostete das Unternehmen € 1.800 Erlösausfall pro Lkw.
Was machte das finanziell aus? Durch die Verwendung von Schmierstoff einer schlechteren Qualität und die nicht erfolgte Optimierung der Ölwechselintervalle führte man jedes Jahr einen unnötigen Ölwechsel durch, der sie etwa € 82.000 an Öl und Filter kostete. Und man hatte einen Erlösausfall von 1 Tag pro Lkw pro Jahr durch wartungsbedingte Stillstandzeiten, was sich auf € 1,8 Mio. für die Flotte summierte. Und weil man ein Öl verwendete, das die Kraftstoffeffizienz nicht erbrachte, verschwendete man € 588 pro Jahr pro Lkw bzw. € 588.000 allein für Kraftstoff – etwas 1,7 % der jährlichen Gesamtkosten für Kraftstoff.
Das positive Ende war, dass diese Bewertung potenzielle Kostensenkungen von etwa € 2,4 Mio. pro Jahr aufdeckte, die durch eine Optimierung der Ölwechselintervalle, der Kraftstoffeffizienz und der Ausfallzeiten erreichbar wurden.
Sicher ist es eine große Herausforderung, bei den neuesten Trends auf dem Laufenden zu bleiben, wie z. B. dem Übergang hin zu Ölen mit niedrigerer Viskosität, die Gesetzgebung zu Treibhausgasen, neue OEM-Spezifikationen und die Optimierung von Ölwechseln. Viele Flottenmanager haben jedoch Millionen Euro gespart, dadurch dass sie die spezifischen Anwendungen ihrer Flotte bewertet und definiert haben, und weil sie mit dem optimalen Schmierstoff die Wartungsintervalle verlängern konnten. Dies verbessert wiederum geschäftliche Zielsetzungen wie Service-Verfügbarkeit, Kilometerleistung pro Lkw, Ladungsmasse pro Kilometer und längere Lebensdauer der Ausrüstung.
Mit der Beratung von Experten zu neuen Technologien, in Kombination mit Testprotokollen, können Sie die richtigen Produkte identifizieren, die zur Optimierung von Ölwechselintervallen, Kraftstoffeffizienz und Ausfallzeiten führen. Und Sie werden die Sicherheit zu schätzen wissen, dass Sie Ihre Flotte konsistent mit OEM-Empfehlungen eingesetzt und dabei ihre Leistungsfähigkeit maximiert wird.